Scientists at Stanford have created a new device that can perform dynamic tasks with significantly less energy than before.
As machines continue to advance, they are being tasked with more and more complex and dynamic responsibilities. This includes creating powered prostheses for amputees and developing robots capable of navigating the outside world. However, the traditional electric motor was originally intended for consistent, continuous tasks such as operating a compressor or rotating a conveyor belt. Even with recent advancements, these motors still consume a significant amount of energy when performing more intricate movements.
Scientists at Stanford University have developed a method to enhance the performance of electric motors by incorporating a novel actuator, a device that utilizes energy to facilitate movement. This innovation significantly improves the efficiency of motors when executing dynamic motions. The actuator they developed, which was featured in a publication in Science Robotics on March 20, utilizes springs and clutches to efficiently perform a range of tasks while consuming significantly less energy compared to a conventional electric motor.
“Instead of consuming excessive electricity while idling and producing heat, our actuator utilizes clutches to achieve the impressive efficiency levels observed in electric motors during continuous operations without compromising on controllability and other appealing features,” stated Steve Collins, a mechanical engineering associate professor and the senior author of the paper.
Springing into action
The actuator operates by utilizing the power of springs to generate force without consuming energy. Springs have the inherent property of resisting elongation and strive to return to their original length when released. When the actuator is lowering something heavy, the researchers can activate the springs to stretch and alleviate some of the load on the motor. By securing the springs in the extended position, the energy can be stored for future use in supporting the motor with another task.
A series of electroadhesive clutches make it possible to engage and disengage the springs efficiently. Every rubber spring is positioned between two clutches: one that links the spring to the joint to provide support for the motor, and another that secures the spring in a stretched position when it is not in use.
These clutches are made up of two electrodes that smoothly slide past each other when they are not in use. One electrode is attached to the spring, while the other is attached to the frame or motor. When activating a clutch, the researchers utilize a significant voltage on one of its electrodes. The electrodes are brought together with a noticeable sound, reminiscent of a more rapid and powerful manifestation of the static electricity that causes a balloon to adhere to a wall when it is rubbed against a carpet. Releasing the spring is a straightforward process of grounding the electrode and reducing its voltage to zero.
“They are lightweight, compact, highly energy efficient, and have rapid on-off capabilities,” stated Erez Krimsky, the lead author of the paper, who recently finished his PhD in Collins’ lab. “And with a deep understanding of the mechanics involved, it presents a myriad of fascinating opportunities to manipulate and direct the behavior of clutched springs, resulting in captivating and unique results.”
Six clutched springs enhance the motor in the Collins and Krimsky-developed actuator. These springs can be engaged in various combinations. The researchers subjected the design to a battery of demanding motion tests, encompassing rapid acceleration, varying loads, and seamless, consistent movement. For each task, the augmented motor demonstrated a remarkable decrease in power usage compared to a standard electric motor. In fact, it consumed 50 percent less power at minimum and, in the most impressive scenario, reduced power consumption by a staggering 97 percent.
Enhanced motors with advanced capabilities
With the help of advanced motors, robots can extend their range and increase their productivity. An extended battery life for a robot would greatly enhance its capabilities, allowing it to perform more significant tasks without interruption. There are numerous risky situations, such as those involving toxic materials, hazardous environments, or other dangers, where it is much safer to deploy a robot rather than putting a person at risk.
“This also has implications for assistive devices such as prosthetics or exoskeletons,” Krimsky mentioned. “If they don’t require frequent recharging, they can greatly benefit the users.”
At present, the actuator’s controller requires a few minutes to calculate the optimal utilization of springs for a new task. However, the researchers are actively working on significantly reducing this timeframe. They have a vision for a system that can learn from past tasks, building a database of more efficient movements over time. With the help of artificial intelligence, it can then figure out how to effectively tackle new challenges.
“We have identified several minor adjustments in control and design that we would like to implement. However, we believe that the technology has reached a stage where it is prepared for commercial application,” Collins stated. “We would be thrilled to explore the possibility of commercializing this technology and establishing a company to manufacture these advanced actuators for the next generation of robots.”
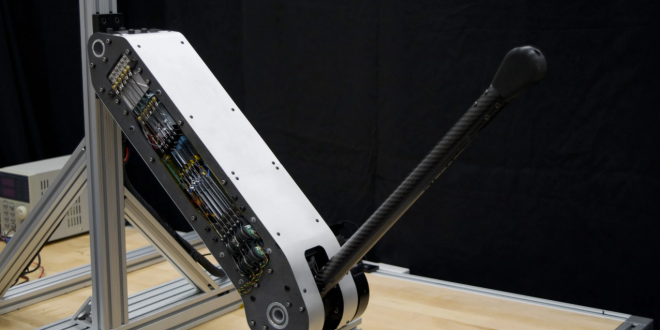